Tunnel Kilns
The terminology Tunnel Kiln refers to all kilns that are of a continuous operational nature. Tunnel kilns provide the very best opportunity for fuel efficiency and cost effective operation where mass production is required.
As can be seen from the summary selection of Tunnel Kilns depicted here, we have manufactured everything from small electric or gas pusher furnaces / kilns right up to wide and long Tunnel kilns for the sanitaryware or brick industries.
We have manufactured kilns for installation in every continent and most countries worldwide. Our team is experienced in handling small and large projects with the same dedication to detail our clients expect.
We deliver on time, in budget, and "proven in production"
CFD
Computational Fluid Dynamics
Leveraging advanced CFD simulations, we deliver intricate furnace solutions tailored for peak performance — specializing in process and design enhancements to elevate your high-end products.
This has several advantages:
- Enhancing the operational efficiency of your thermal systems
- Piloting groundbreaking concepts for your production furnace's functionality
- crafting and showcasing your tailor-made manufacturing facility
Over time, the reliance on computer-aided calculation methods has surged, marking a significant shift in how we approach design and efficiency. At THERSER, we harness the power of cutting-edge flow simulation techniques, merging them with our extensive technical knowledge and hands-on experience. This synergy, powered by CFD simulations, enables us to forge thermal processes and kiln designs that are not only highly efficient and lifelike but also remarkably reliable and fail-proof.
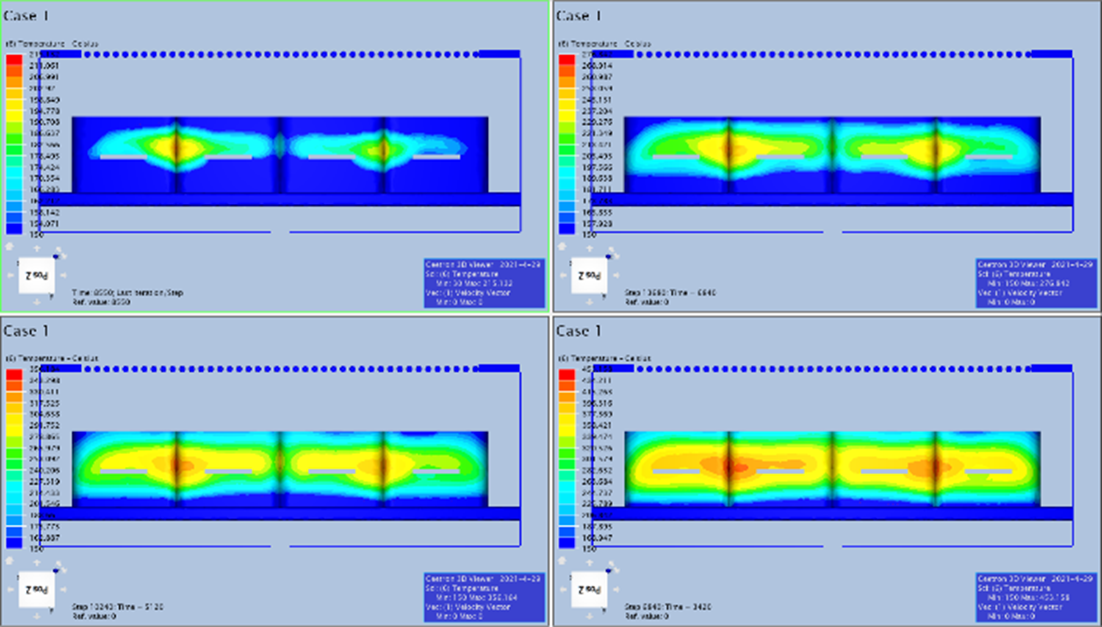
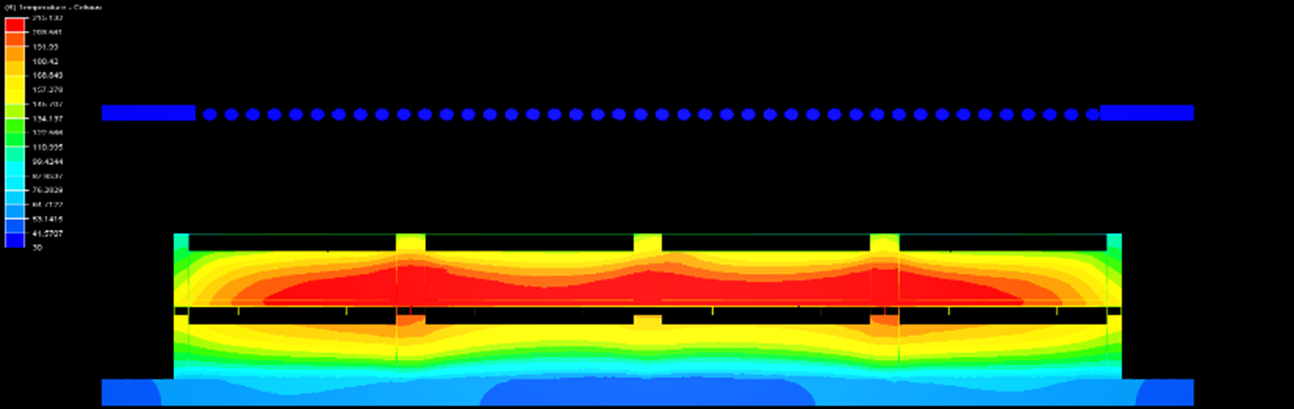
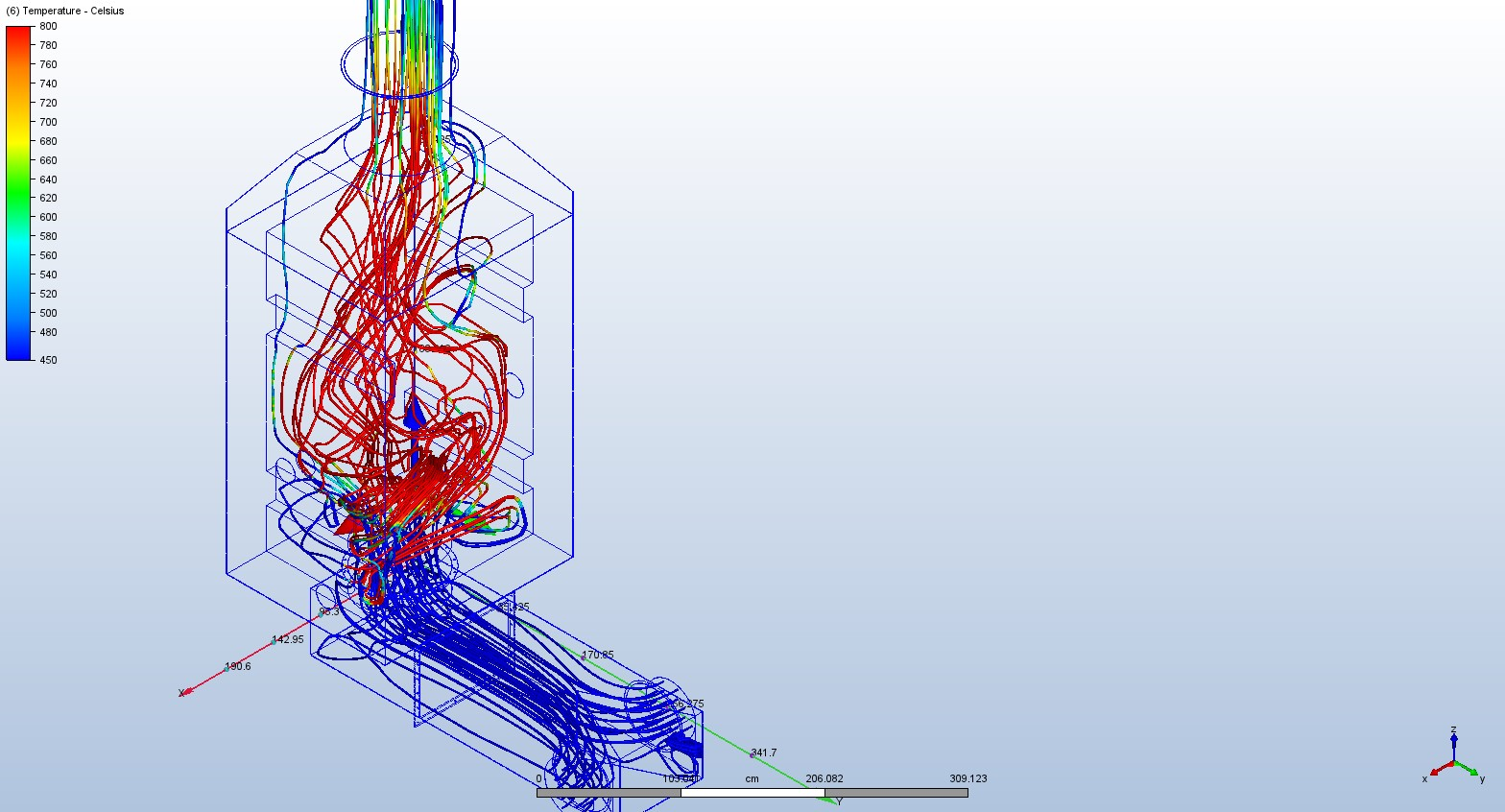
Computational Fluid Dynamics (CFD) is a powerful tool used to simulate and analyze fluid flows, heat transfer, and associated phenomena in various engineering applications. Using CFD to analyze the performance of a kiln in terms of air flow, heat transfer, and other dynamic interactions offers several advantages:
Enhanced Understanding of Flow Dynamics: CFD provides detailed visualization and analysis of air flow within the kiln. This includes velocity, temperature distributions, and patterns that are difficult to measure during operation. Understanding these dynamics helps in optimizing the airflow for uniform temperature distribution and efficient heat transfer.
Design Optimization: Before physical modifications are made to the kiln, CFD allows for the simulation of various design changes. Engineers can test the effects of altering the shape, size, or position of inlets and outlets, or modifying internal structures, to determine the best configuration for optimal performance.
Improved Thermal Efficiency: By analyzing heat transfer within the kiln, CFD helps in identifying cold and hot spots and areas of heat loss. This information can be used to improve the kiln’s insulation, adjust the heating mechanisms, and ultimately enhance the kiln’s thermal efficiency.
Reduced Energy Consumption: Optimizing airflow and heat transfer not only improves the quality of the output but can also lead to significant reductions in energy use. Efficient airflow ensures that less fuel is needed to maintain the required temperatures, thereby reducing operational costs.
Emission Control: CFD simulations can help predict and reduce the emission of pollutants by optimizing combustion conditions and airflow in the kiln. This is crucial for meeting environmental regulations and reducing the kiln’s environmental impact.
Safety Improvements: CFD analysis can identify potentially dangerous conditions within the kiln, such as areas prone to overheating or excessive pressure build-up. This helps in taking preemptive measures to enhance safety for operators and reduce the risk of accidents.
Scalability and Experimentation: CFD allows for the testing of kiln performance under various operational conditions without the need for expensive and time-consuming physical trials. This includes scalability studies to understand how changes in scale (e.g., from pilot scale to full production) impact performance, allowing for more confident upscaling.
CFD in the analysis and optimization of kiln performance leads to a deeper understanding of the complex interactions within the kiln, contributing to better design, operation, and maintenance strategies.
TUNNEL KILNS
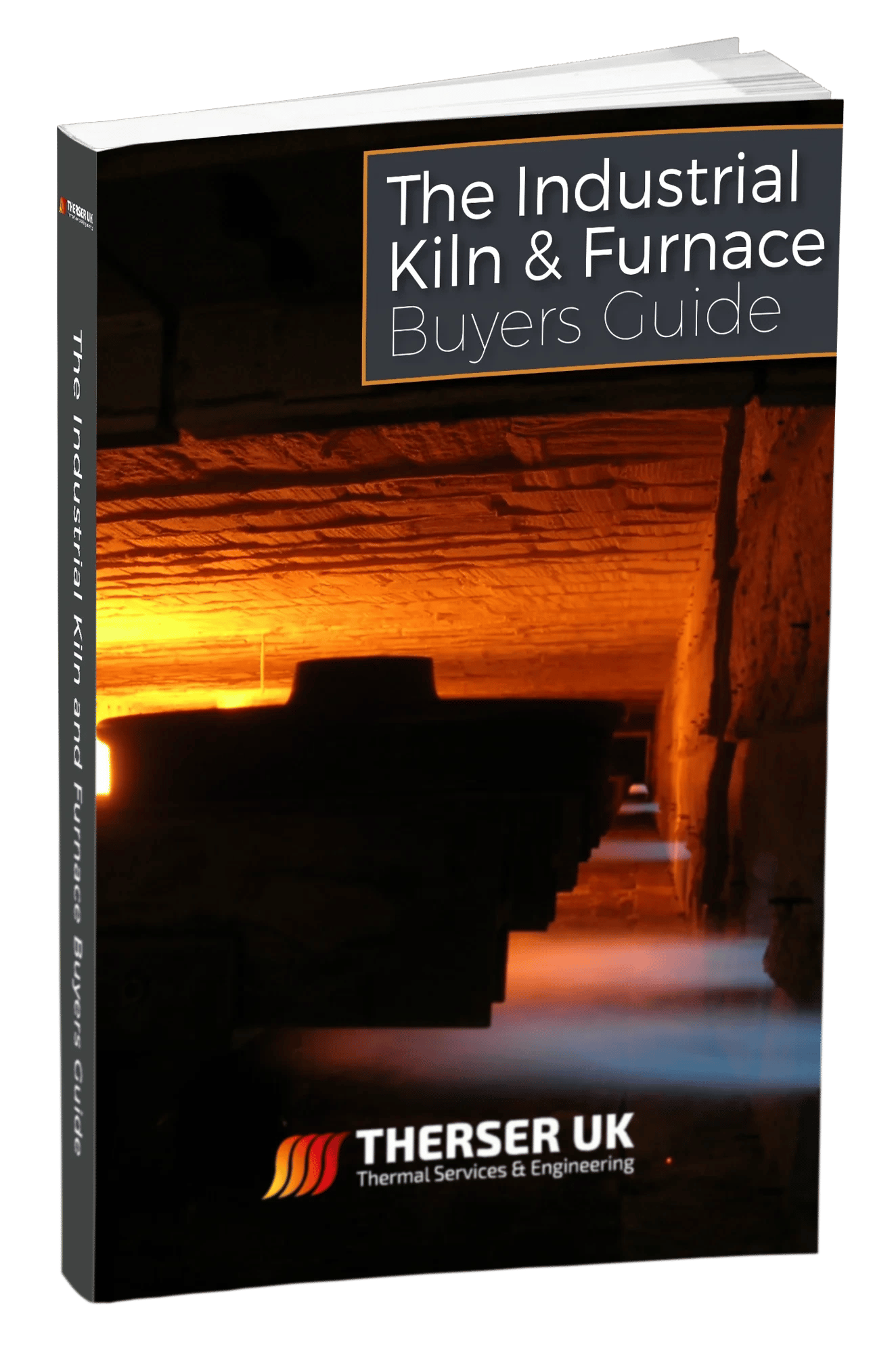
DOWNLOAD THE INDUSTRIAL KILN & FURNACE BUYERS GUIDE
If you need, or may need in the future, to invest in an industrial kiln, furnace or oven, then get a copy of this FREE guide today.
Discover:
- How to choose the right type of kiln or furnace
- How to avoid the most common mistakes with industrial kilns and furnaces
- How to ensure maximum fuel efficiency
So confirm your correct email address using the form provided and your copy will be in your inbox within seconds!
OUR CERTIFICATIONS
REVIEWS
TALK TO US TODAY
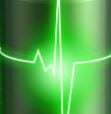
