Advanced Furnace Technologies
Furnaces are more than just equipment—they are the heart of thermal processing in industries where precise heating is crucial for success. In sectors such as metalworking, where the transformation of raw materials into high-value products hinges on meticulous temperature control, furnaces stand as indispensable tools. The term "furnace" in the Metals Industry is not merely a label; it is a testament to the critical role these sophisticated systems play in driving industrial progress.
At Therser UK, we bring decades of expertise in furnace technologies to the table, offering an extensive range of solutions tailored to meet the diverse needs of modern industries. Whether you're working with electrically heated systems that require exact temperature control or gas-heated systems designed for large-scale operations, our adaptability and deep understanding of thermal processing make us a leader in the field. Our advanced furnace solutions are designed to meet the specific demands of your industry, ensuring optimal performance and reliability.
Our technology seamlessly bridges the gap between kilns and furnaces, underscoring a common principle—the mastery of heat to achieve precise outcomes. This expertise is the culmination of years of innovation, rigorous testing, and a deep dive into the thermal dynamics that govern industrial processes. Our portfolio, rich with success stories, spans installations across the globe—from the thriving industrial hubs of the UK, France, Spain, and Nigeria to the innovation-driven landscapes of the USA and the rapidly expanding markets of China. Each project is a testament to our ability to deliver excellence in any setting, under any conditions.
But our commitment to your success goes beyond simply supplying equipment. We immerse ourselves in the nuances of each project, taking the time to understand your unique challenges and requirements. Whether you're looking for compact units designed for specialized applications or large-scale installations capable of supporting mass production, our approach is consistent—meticulous attention to detail, unwavering dedication to your specifications, and a commitment to delivering solutions that not only meet but exceed your expectations.
Every project we undertake is guided by a simple yet powerful promise: to deliver solutions that are on time, within budget, and proven in real-world production environments. This relentless pursuit of excellence, coupled with our vast experience and global reach, makes Therser UK your ideal partner for furnace solutions that are not just effective but transformative. With Therser UK, your operations will run more efficiently, your products will achieve the highest standards of quality, and your business will be positioned for long-term success in an ever-evolving industrial landscape.
Heat treatment processes in furnaces involve controlled heating and cooling of materials, typically metals, to alter their physical and mechanical properties without changing their shape. The process is widely used to improve hardness, strength, ductility, and toughness. Different heat treatment processes are applied based on the desired material properties. Here are some common heat treatment processes performed in furnaces:
Annealing
- Purpose: Soften the material, improve ductility, relieve internal stresses, and refine grain structure.
- Process: The metal is heated to a specific temperature (often above its recrystallization temperature), held there for a certain period, and then cooled slowly (usually in the furnace itself).
- Materials: Widely used for steel, copper, aluminum, and brass.
Normalizing
- Purpose: Refine grain structure, improve toughness, and relieve internal stresses.
- Process: The material is heated to a temperature higher than in annealing, held at that temperature, and then air-cooled.
- Materials: Commonly used for carbon steel and alloy steel.
Hardening (Quenching)
- Purpose: Increase hardness and strength.
- Process: The metal is heated to its austenitizing temperature (high enough to form austenite), then rapidly cooled (quenched) in water, oil, or air, depending on the material.
- Materials: Typically used for steels that contain sufficient carbon and other alloying elements to form martensite.
Tempering
- Purpose: Reduce brittleness and internal stresses caused by hardening, while retaining a significant level of hardness.
- Process: After hardening, the material is reheated to a lower temperature (below its critical point) and then cooled.
- Materials: Used for hardened steel.
Carburizing
- Purpose: Increase surface hardness by adding carbon to the outer layer of the metal while maintaining a softer core.
- Process: The material is heated in a carbon-rich environment (like in gas or solid carburizing agents), allowing carbon atoms to diffuse into the surface.
- Materials: Often applied to low-carbon steel to improve surface hardness while retaining ductility inside.
Case Hardening
- Purpose: Similar to carburizing, case hardening hardens the surface of a metal while maintaining a tough and ductile core.
- Process: In addition to carburizing, processes like nitriding (diffusion of nitrogen) and carbonitriding (diffusion of both carbon and nitrogen) are employed to harden the outer layer.
- Materials: Typically used for gears, bearings, and camshafts.
Solution Heat Treatment
- Purpose: Homogenize the material and dissolve alloying elements to improve strength and corrosion resistance.
- Process: The material is heated to a high temperature (solutionizing temperature) to dissolve precipitates and is then quenched to retain the solutionized structure.
- Materials: Commonly used for aluminum and stainless steel.
Precipitation Hardening (Age Hardening)
- Purpose: Increase strength by forming small, dispersed particles within the metal matrix.
- Process: The material is heated to an intermediate temperature to allow controlled precipitation of alloying elements and then cooled.
- Materials: Common for aluminum alloys, nickel-based superalloys, and some stainless steels.
Stress Relieving
- Purpose: Reduce internal stresses introduced by welding, machining, or other processes without significantly altering the material's structure.
- Process: The material is heated to a moderate temperature (lower than that used in annealing), held at that temperature, and then cooled.
- Materials: Used for steel, aluminum, and copper alloys.
Austempering
- Purpose: Produce a more ductile and tough structure (bainite) rather than the brittle martensite formed by conventional quenching.
- Process: The metal is heated, then quenched in a bath held at a temperature just above the martensite start temperature, allowing bainite to form instead of martensite.
- Materials: Typically used for ductile iron and certain steels.
Martempering (Marquenching)
- Purpose: Reduce the formation of internal stresses and distortion, while still producing martensite.
- Process: The material is quenched to a temperature just above the martensite formation range, held at that temperature, and then allowed to air-cool slowly.
- Materials: Often used for steel parts that require a balance of strength and toughness with minimal distortion.
Nitriding
- Purpose: Enhance surface hardness and wear resistance by introducing nitrogen into the surface layer.
- Process: The material is heated in a nitrogen-rich environment (gas or plasma) at temperatures lower than traditional carburizing.
- Materials: Common for steel, particularly alloy steels.
Vacuum Heat Treatment
- Purpose: Prevent oxidation and contamination of the material during heat treatment.
- Process: Heat treatment is performed in a vacuum chamber where the absence of air prevents oxidation.
- Materials: Often used for high-grade tool steels and aerospace components.
Each of these processes can be performed in various types of furnaces, such as:
- Box furnaces (for general heating and large workpieces),
- Induction furnaces (for localized heating),
- Vacuum furnaces (to prevent oxidation),
- Fluidized bed furnaces (for more uniform heating),
- Continuous furnaces (for mass production).
Understanding the specific material and desired properties helps determine the most suitable heat treatment process. This is where we can help with your needs
FURNACES
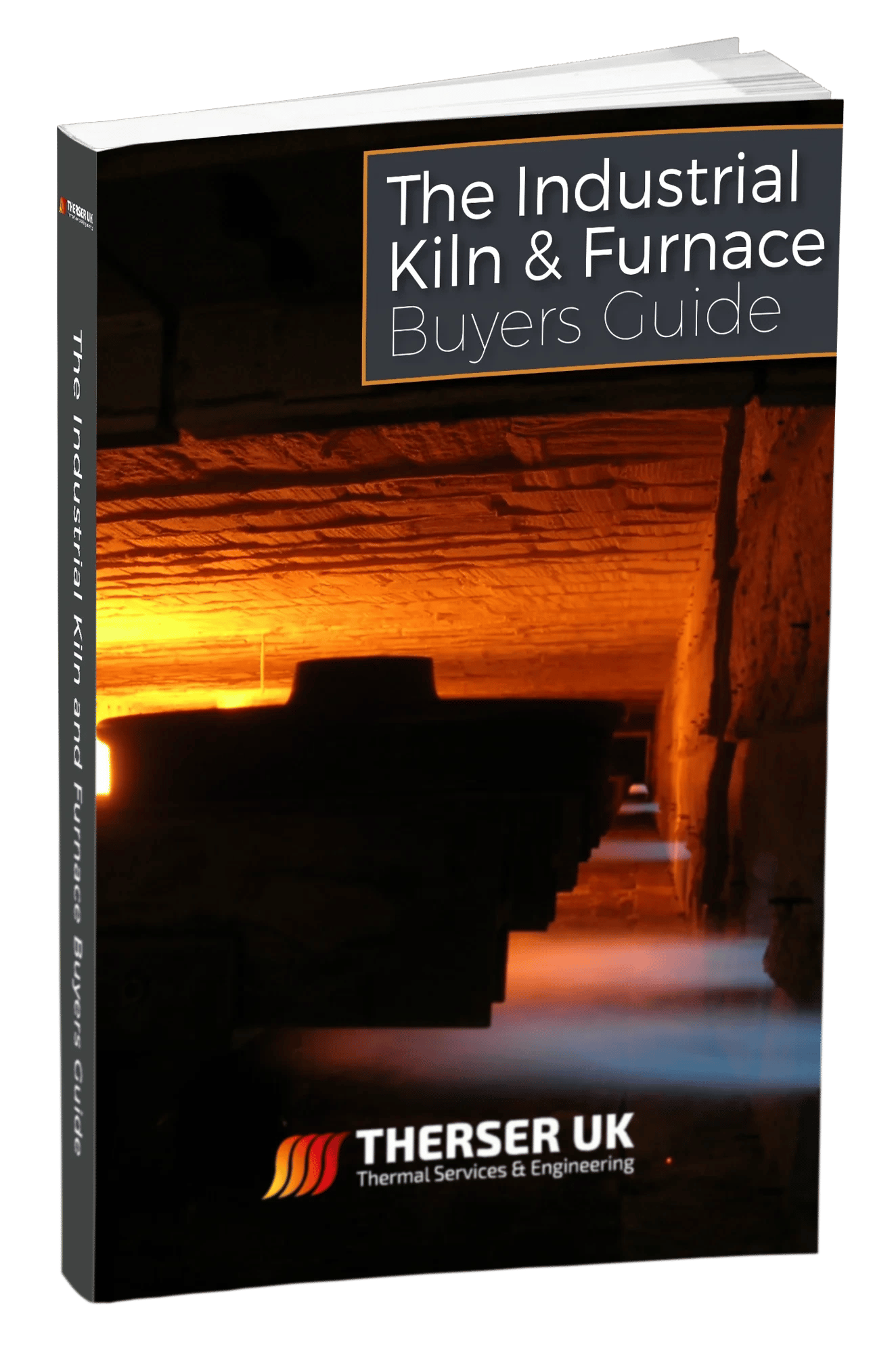
DOWNLOAD THE INDUSTRIAL KILN & FURNACE BUYERS GUIDE
If you need, or may need in the future, to invest in an industrial kiln, furnace or oven, then get a copy of this FREE guide today.
Discover:
- How to choose the right type of kiln or furnace
- How to avoid the most common mistakes with industrial kilns and furnaces
- How to ensure maximum fuel efficiency
So confirm your correct email address using the form provided and your copy will be in your inbox within seconds!
OUR CERTIFICATIONS
REVIEWS
TALK TO US TODAY
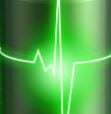
