Mild Steel Fabrication
Therser UK offer a custom fabrication service for insulation, combustion systems, control systems, and exhaust maintenance – as well as complete kilns and furnaces and any custom-made fabrication that your company requires.
Each component or system is designed and manufactured according to your specifications by our UK based engineering team.
How It Works
Our fabrication service is completely customer focused, encompassing the full process from concept to product testing, through to installation and after sales support. Commissioning bespoke fabrication work from Therser is fast and efficient. Our engineers use AutoCAD software to design your component, allowing regular communication with our customers prior to the manufacturing stage. Component designs can be tweaked and modified according to your requirements and put through rigorous virtual testing to ensure high performance
Your new equipment is pre-assembled in our factory, where it is inspected, and product tested prior to delivery. We supervise your on-site installation in a sensitive manner with as little disruption to your schedule as possible. Each commission also comes with full product training and after sales support as standard.
As a heat treatment specialist, we are often asked about the various standards and codes there are in the field of welding. Given that we provide furnaces and kilns for sensitive sectors like the aerospace industry, sanitaryware manufacturers and solar energy businesses –among others – welding quality is a question that crops up again and again. This is why we are proud to have been certified under the demanding BS.EN.ISO 9606-1 standards for welding quality
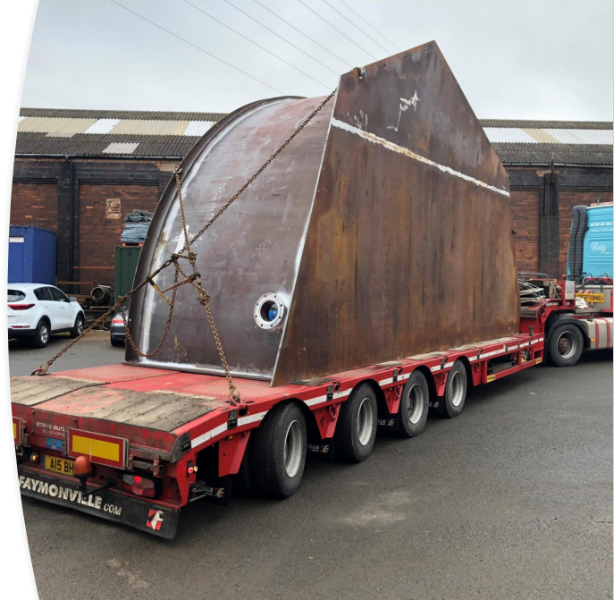
The Advantage of BS.EN.ISO 9606-1 standard
All these welding methods can be employed in our work, but the most relevant technique is fusion welding, which is the area of competence covered by BS.EN.ISO 9606-1. This is a harmonised standard, meaning it complies with standards expected under BS, ISO and CEN rules. In other words, a kiln fusion welded under BS.EN.ISO 9606-1 criteria can safely be used anywhere in the world.
It takes high-quality workmanship to be able to weld to the rigorous standards of any ISO accreditation, including 9606-1. Any customers who want to know their welding processes – whether they are arc welds, laser welds, induction welds, oxyfuel or solid reactant welds – are being carried out by a fully accredited contractor should seek out a BS.EN.ISO 9606-1 compliant manufacturer.
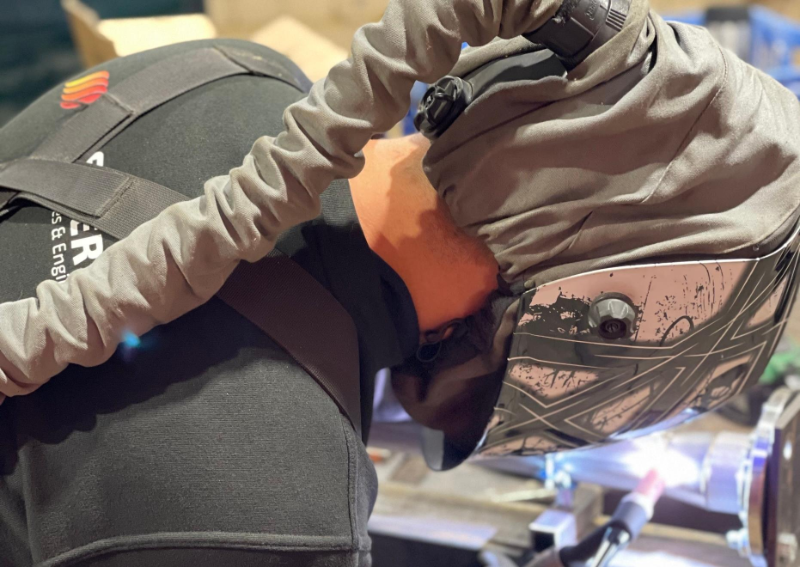
Heavy Fabrication
The heavy fabrication process involves a number of different steps, including design, material selection, cutting, welding, bending, and finishing. Each of these steps requires specialized equipment and skilled technicians to ensure that the final product meets the necessary specifications and quality standards.
One of the key advantages of heavy fabrication is its ability to produce structures that are both strong and durable. Because these structures are often exposed to extreme conditions, such as high winds, heavy rain, and corrosive materials, it is essential that they are able to withstand these forces and remain intact over time. Heavy fabrication techniques and materials are specifically designed to provide this level of strength and durability, making them an essential part of many construction and manufacturing projects.
Another benefit of heavy fabrication is its versatility. With the use of computer-aided design (CAD) and advanced machinery, it is possible to create a wide variety of shapes and sizes, allowing for the creation of complex structures that would be difficult or impossible to produce using traditional methods. This versatility makes heavy fabrication ideal for a range of applications, from building bridges and offshore platforms to manufacturing large industrial equipment and machinery.

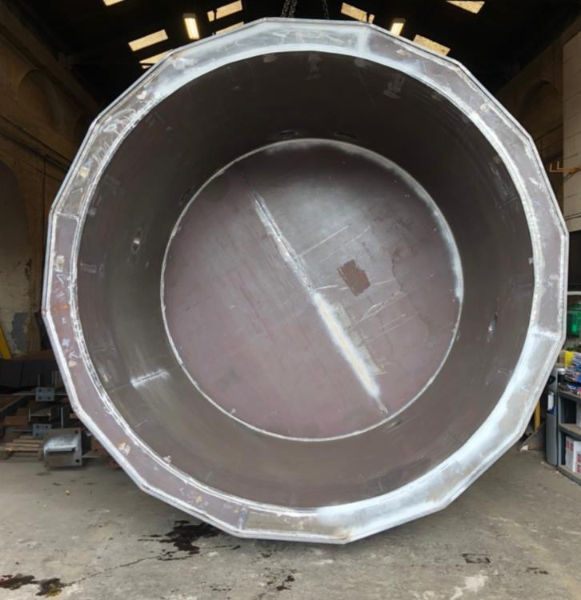
Fabrication Processes We can Offer
Welding: Welding is a process of joining two or more pieces of metal together using heat and/or pressure. The heat can be generated by a flame, an electric arc, or a laser. Welding can be used to create structures, repair damaged components, or add additional material to existing components. There are several types of welding processes, including MIG (metal inert gas) welding, TIG (tungsten inert gas) welding, stick welding, and gas welding.
Extrusion: Extrusion is a process of forcing a material through a die to create a long, continuous shape with a constant cross section. The material can be metal, plastic, or rubber. Extrusion can be used to create products such as tubing, rods, and profiles.
Sheet metal fabrication: Sheet metal fabrication is a process of cutting, bending, and forming thin sheets of metal to create various products. Sheet metal can be cut using laser cutting, waterjet cutting, or shearing. Bending can be done using press brakes or roll forming. Forming can be done using punching or stamping.
3D printing: 3D printing is a process of creating objects by layering material using a 3D printer. The printer reads a digital file and creates the object by depositing material layer by layer. 3D printing can be used to create complex geometries, prototypes, and custom parts.
Welding types
MIG welding (Metal Inert Gas): MIG welding is easy to learn, versatile, and can be used on a wide range of metals, including aluminum and stainless steel. It produces high-quality welds with good penetration and minimal spatter, making it a popular choice for both DIY and professional welding projects.
TIG welding (Tungsten Inert Gas): TIG welding produces extremely high-quality welds with precise control over the heat input and weld puddle. It can be used on a wide range of materials and thicknesses and is often used for precision welding of delicate or complex parts.
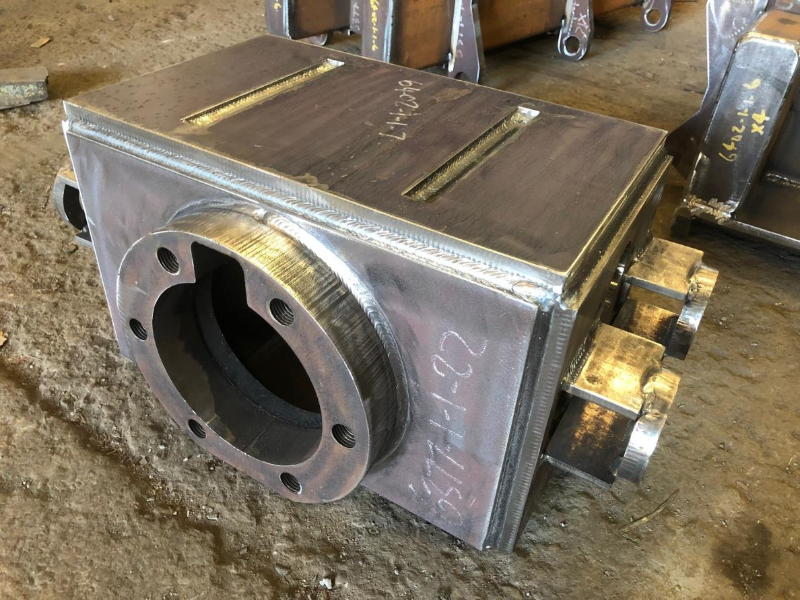
Stick welding (Shielded Metal Arc Welding): Stick welding is a versatile and inexpensive welding method that can be used on a wide range of materials and in outdoor or windy conditions. It is often used in construction, maintenance, and repair projects.
Flux-cored welding: Flux-cored welding uses a continuously fed wire electrode that contains a flux core, eliminating the need for a separate shielding gas. It is often used for welding thick or dirty materials and is a popular choice for outdoor and field welding applications.
Gas welding: Gas welding uses a flame to heat and melt the metal, which is then joined using a filler rod. It is a versatile welding method that can be used on a wide range of materials, but it requires a high degree of skill and experience to produce high-quality welds.
What Jobs Therser Can Do. What Code And Processes Do We Adhere To
A Step-by-Step Guide to Heavy Fabrication: Processes, Testing, and Stages
Heavy fabrication is a specialized area of metal fabrication that involves the manufacturing of large-scale and heavy-duty structures and components. It encompasses various processes and stages to transform raw materials into finished products. In this step-by-step guide, we will explore the key stages involved in heavy fabrication, providing insights into the processes, testing, and considerations at each step. Whether you are new to heavy fabrication or seeking to expand your knowledge, this guide will help you navigate the complex world of fabricating heavy structures.
Step 1: Project Planning and Design
Understand project requirements: Begin by comprehending the project specifications, including dimensions, load-bearing capacity, and intended use of the fabricated structure.
Design and engineering: Collaborate with design and engineering teams to develop detailed drawings and models, ensuring the structural integrity and feasibility of the fabrication project.
Material selection: Choose appropriate materials, considering factors such as strength, corrosion resistance, and suitability for the application.
Step 2: Material Preparation
Material procurement: Source the required materials, ensuring they meet the specified standards and quality requirements.
Material inspection: Perform visual and non-destructive testing (NDT) techniques to ensure the material's integrity and detect any defects or imperfections.
Material cutting: Use specialized equipment, such as saws, plasma cutters, or lasers, to accurately cut the raw materials according to the project specifications.
Step 3: Forming and Shaping
Plate bending and rolling: Utilize plate bending machines or rolling mills to bend or curve metal plates into the desired shapes and contours.
Section bending: Employ specialized machines to bend or form structural sections, such as beams or channels, to the required profiles.
Weld preparation: Prepare the edges of the fabricated components for welding by beveling, chamfering, or machining as necessary.
Step 4: Welding and Assembly
Assembly: Fit and align the fabricated components accurately, ensuring proper positioning and dimensional accuracy.
Welding techniques: Employ appropriate welding methods, such as MIG (Metal Inert Gas) welding, TIG (Tungsten Inert Gas) welding, or submerged arc welding, to join the fabricated components.
Welding procedures: Follow established welding procedures and adhere to relevant welding codes and standards for quality assurance.
Step 5: Surface Treatment and Finishing
Surface preparation: Achieve the desired surface finish by grinding, sanding, or polishing the fabricated components.
Surface cleaning: Remove any contaminants, rust, or mill scale from the fabricated structure through processes like abrasive blasting or chemical cleaning.
Protective coatings: Apply suitable coatings, such as paint, powder coating, or galvanizing, to enhance corrosion resistance and durability.
Step 6: Quality Inspection and Testing
Non-destructive testing (NDT): Conduct various NDT techniques, including ultrasonic testing, radiographic testing, or magnetic particle inspection, to detect any defects or discontinuities. These tests can identify flaws that are not visible to the naked eye and ensure the structural integrity of the fabricated components.
Dimensional checks: Verify the dimensional accuracy and alignment of the fabricated components using precise measuring tools and techniques. This includes measurements of lengths, widths, heights, hole positions, and other critical dimensions, comparing them against the design specifications.
Visual inspection: Perform a thorough visual examination of the fabricated structure to identify any surface imperfections, welding discontinuities, or irregularities that may affect its structural integrity or aesthetic appearance.
Weld quality assessment: Inspect and evaluate the quality of welds, checking for proper penetration, fusion, and absence of defects such as cracks, porosity, or undercut.
Dye penetrant testing: Apply a dye penetrant to the surface of the fabricated components to detect surface-breaking defects or cracks. Excess penetrant is then removed, and a developer is applied to visualize any indications.
Pressure testing: Subject the fabricated structure to hydrostatic or pneumatic pressure to ensure its integrity under the expected operating conditions. This test is commonly used for pressure vessels, tanks, and piping systems.
Fatigue testing: Simulate cyclic loading on the fabricated structure to evaluate its resistance to fatigue failure. This test involves applying repeated or varying loads to assess the structure's durability over time.
Welding procedure qualification: Qualify the welding procedures used in the fabrication process by conducting testing on representative mock-up welds. This ensures that the chosen welding procedures meet the specified requirements for the project.
Documentation and traceability: Maintain comprehensive records of all inspections, tests, and quality checks performed during the fabrication process. This documentation helps ensure traceability, compliance with standards, and provides a reference for future inspections or repairs
Step 7: Transport, Installation, and Site Integration
Packaging and logistics: Safely package and transport the fabricated structure to the installation site, considering factors like size, weight, and transportation regulations.
Installation and assembly: Install the fabricated components on-site, ensuring proper alignment and connection with other structural elements.
Integration and testing: Conduct site integration and functional testing to ensure the fabricated structure performs as intended and meets the project requirements.
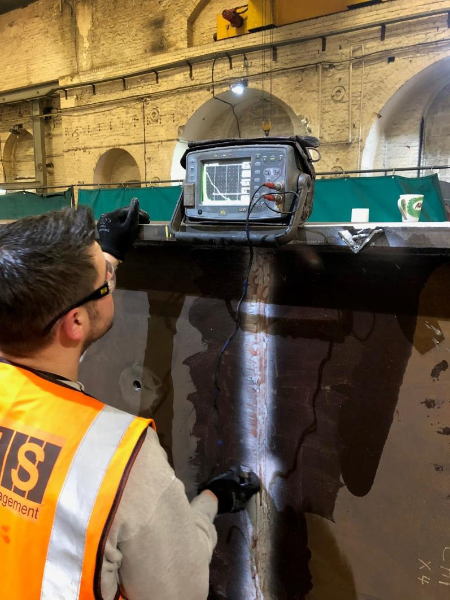
Heavy fabrication involves rigorous quality inspection and testing procedures to ensure the structural integrity, dimensional accuracy, and performance of the fabricated product. Along with non-destructive testing techniques and dimensional checks, visual inspection, weld quality assessment, hardness testing, and other specialized tests help verify the quality of the fabrication. Thorough documentation and traceability further ensure compliance with standards and provide a reference for future inspections or repairs. By implementing comprehensive quality checks and inspections, you can confidently deliver high-quality, reliable heavy fabrications that meet customer specifications and industry requirements.
FABRICATION WELDING
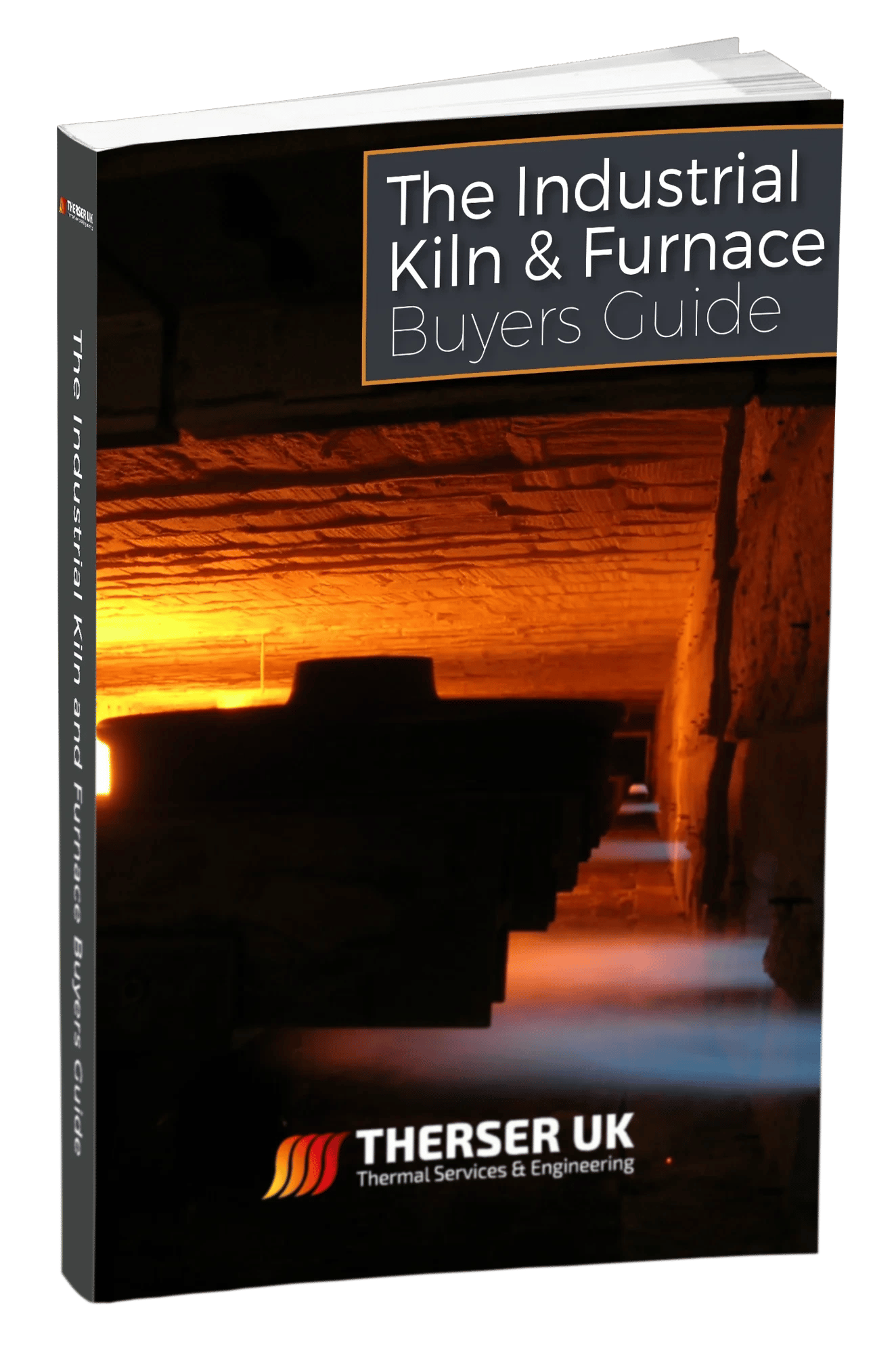
DOWNLOAD THE INDUSTRIAL KILN & FURNACE BUYERS GUIDE
If you need, or may need in the future, to invest in an industrial kiln, furnace or oven, then get a copy of this FREE guide today.
Discover:
- How to choose the right type of kiln or furnace
- How to avoid the most common mistakes with industrial kilns and furnaces
- How to ensure maximum fuel efficiency
So confirm your correct email address using the form provided and your copy will be in your inbox within seconds!
OUR CERTIFICATIONS
REVIEWS
TALK TO US TODAY
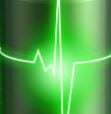
