Therser are the UK’s largest Kiln and Furnace manufacturing company, we are also the only UK company that can offer RHK’s (Roller Hearth Kilns) and SHS’s (Saggar Handling Systems) for various industries and market sectors, including the manufacture of CAM (Cathode Active Materials) for the Lithium-Ion Battery sector which we are currently engaged in with some of our customers.
Therser UK is an established Kiln engineering specialist based in the UK and as such can provide full maintenance and servicing any other type of heat treating equipment that your company may use.
Therser UK has a wealth of experience in the following areas:
- Design and Manufacture of RHK’s, Tunnel Kilns, Rotary Kilns, Furnaces, Driers, Ovens including intermittent, shuttle/top hat, continuous and belt. Fuel gas, electric, oil and LPG.
- Turnkey manufacturing, installation, commissioning and project management services.
- In house design and manufacturing of bespoke, Automation Systems and Handling Systems to meet customer’s requirements.
- 3D modelling design capabilities and VR Interaction capabilities.
- Additive manufacturing printing for rapid prototyping.
- Kiln servicing contracts
- Kiln spare parts
- Any type of equipment relocation and or re-siting.
- Supplying instrument technicians, installation engineers and commissioning engineers.
- Therser can undertake total factory moves or individual pieces of equipment/machinery.
- Project management
What We Offer
•Thermal Process Review and Concept Development: This stage involves a comprehensive assessment of the client's thermal processes and requirements. Based on the review, innovative concepts are developed to optimize efficiency, productivity, and quality.
• Technical Proposal and Formal Quotation: After understanding the client's needs, a detailed technical proposal is prepared, outlining the
suggested solutions and associated costs, culminating in a formal quotation for the project.
• Pre-Engineering to Full Engineering: In this phase, initial pre-engineering is performed to lay the groundwork for the project. As the collaboration progresses, the team transitions to full-scale engineering, finalizing the project's specifications.
• Computational Fluid Dynamics: Computational Fluid Dynamics (CFD) simulations are used to study fluid flow and heat transfer within the
system, optimizing performance and minimizing energy consumption.
• Heat Up and Heat Transfer Thermal Analysis: This analysis assesses the heating and heat transfer mechanisms, allowing for precise control of
temperature profiles and uniformity within the thermal processes.
• 3D Modelling: Utilizing advanced 3D modeling software, a detailed representation of the project is created, aiding visualization and
improving design accuracy.
• Full Refractory Solutions: Comprehensive refractory solutions are offered, providing the appropriate materials and designs to withstand
high temperatures and corrosive environments.
• Electric Element Heating Systems: Electric element heating systems are designed for projects that require precision heating control.
• In-House Full Project Manufacturing Capability: We design and manufacture your project which gives you full control of your design.
• Fully Designed Saggar Handling Systems: Saggar handling systems are carefully designed to safely transport and handle delicate ceramics or other heat-sensitive materials.
• Virtual Reality Tours of Your Project: Clients are offered virtual reality tours, allowing them to experience the project's layout and functionality
before physical construction.
• 3 Off Electrically Fired Test Kilns, with Process Gas Options: In-house test kilns are available for clients to conduct trials and optimize their products' firing processes.
• CAD Drawing and Design: Computer-Aided Design (CAD) drawings are provided, aiding in visualization and facilitating communication throughout the project.
• Project Managed: The entire project is meticulously managed, ensuring timelines are met, and resources are efficiently utilized.
• Test Firings of Your Product: The project includes test firings of the client's product, ensuring it meets the desired specifications and performance criteria.
• In-House PLC Programming: In-house Programmable Logic Controller (PLC) programming enables customized automation and control solutions.
• In-House Panel Building: The fabrication of electrical panels is done in-house, ensuring quality control and efficient integration of control
systems.
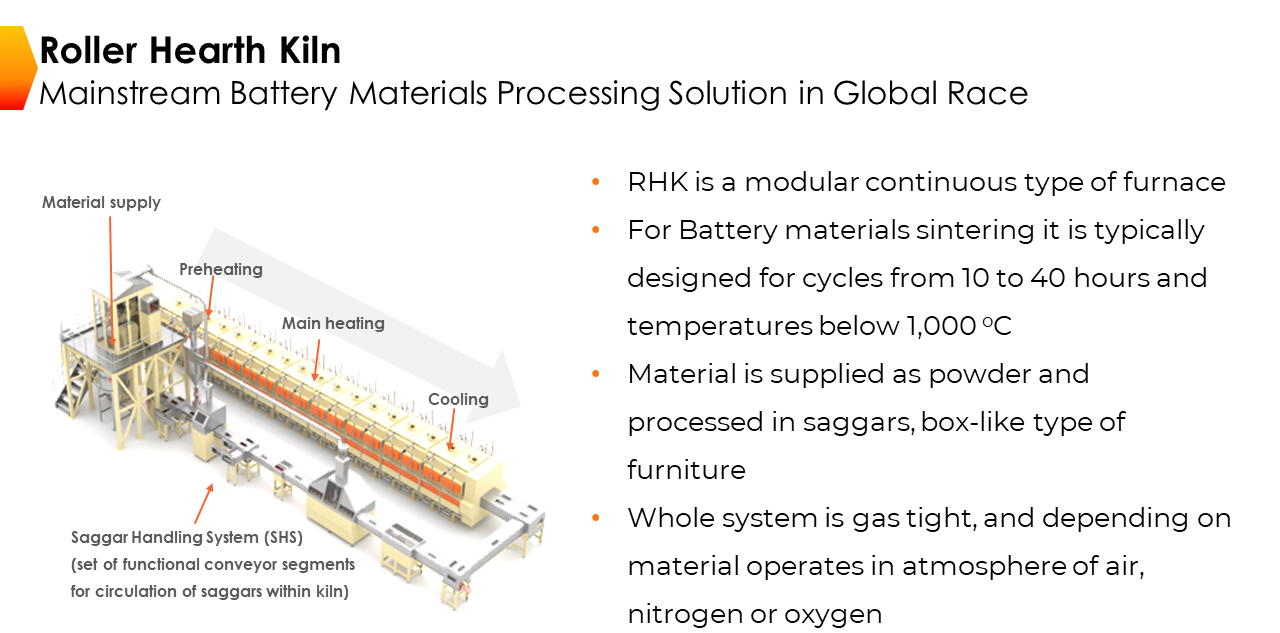
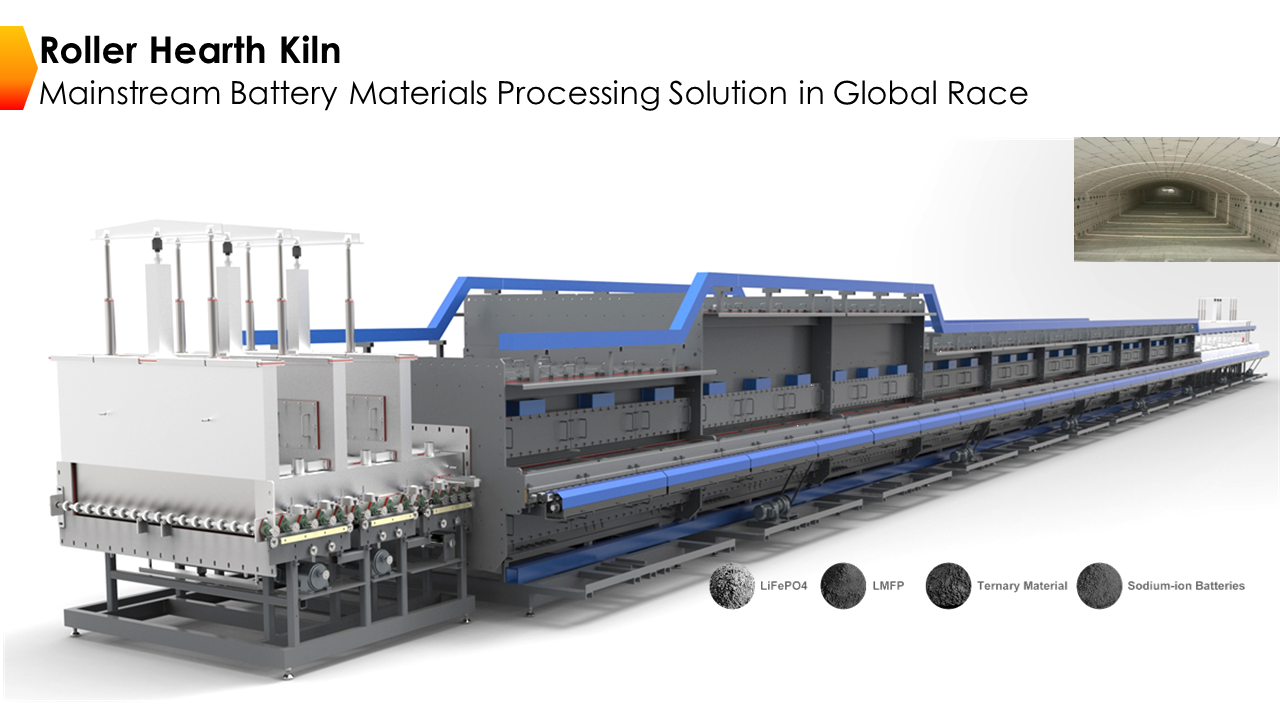
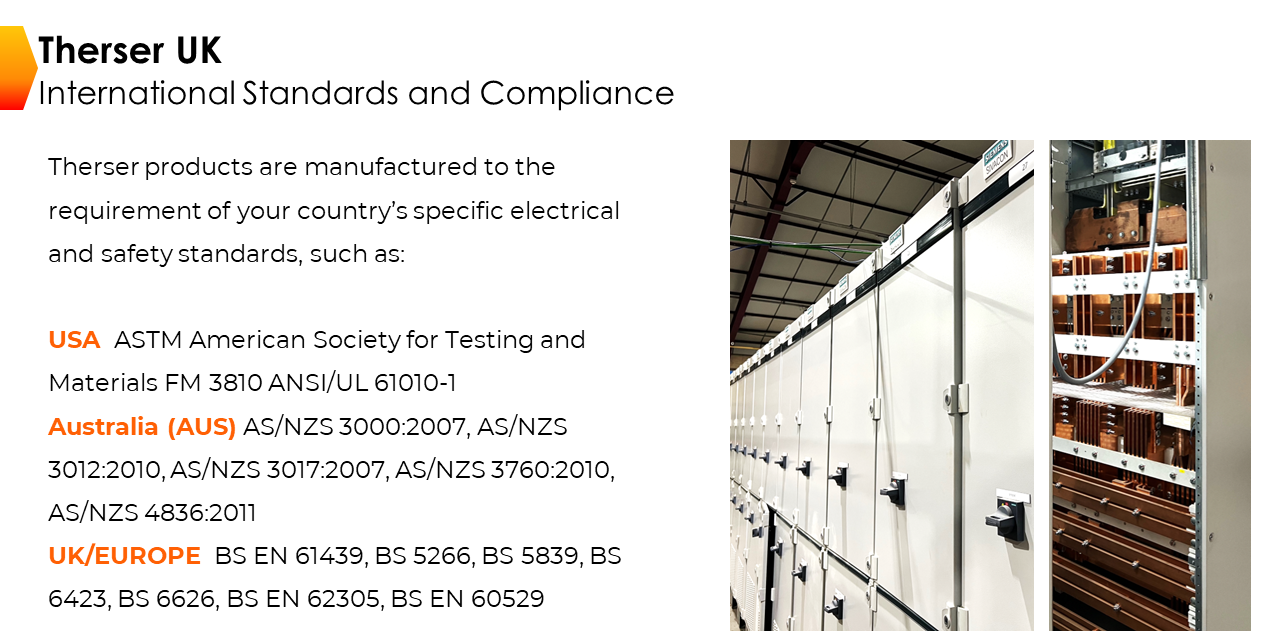
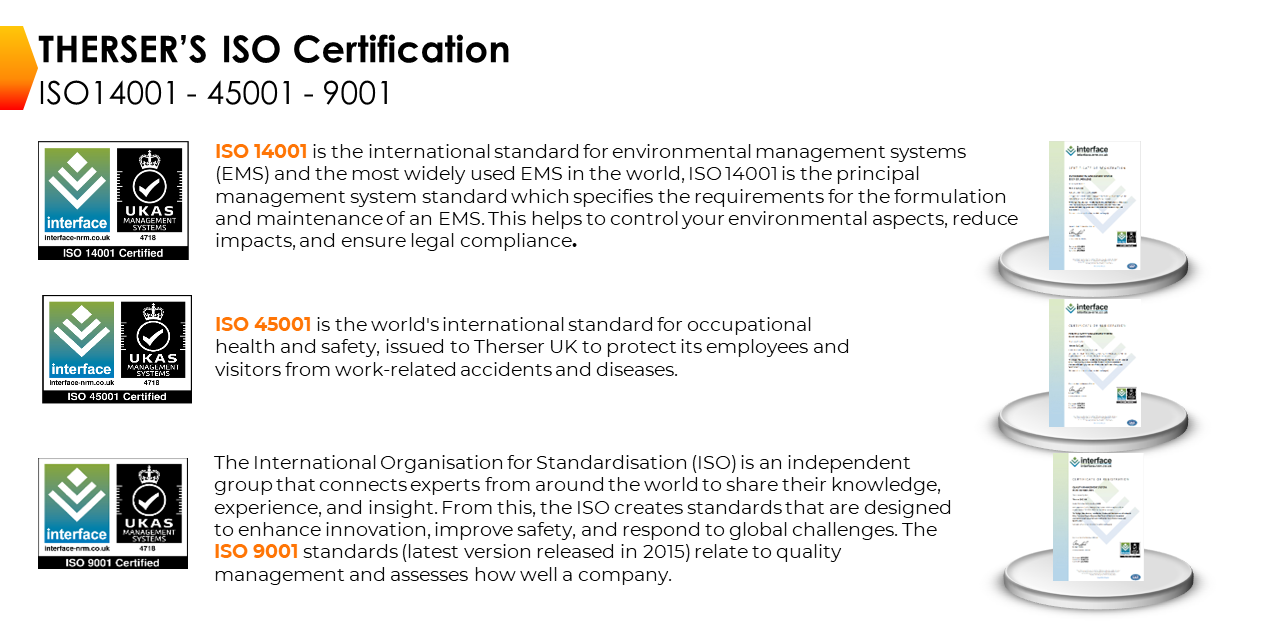
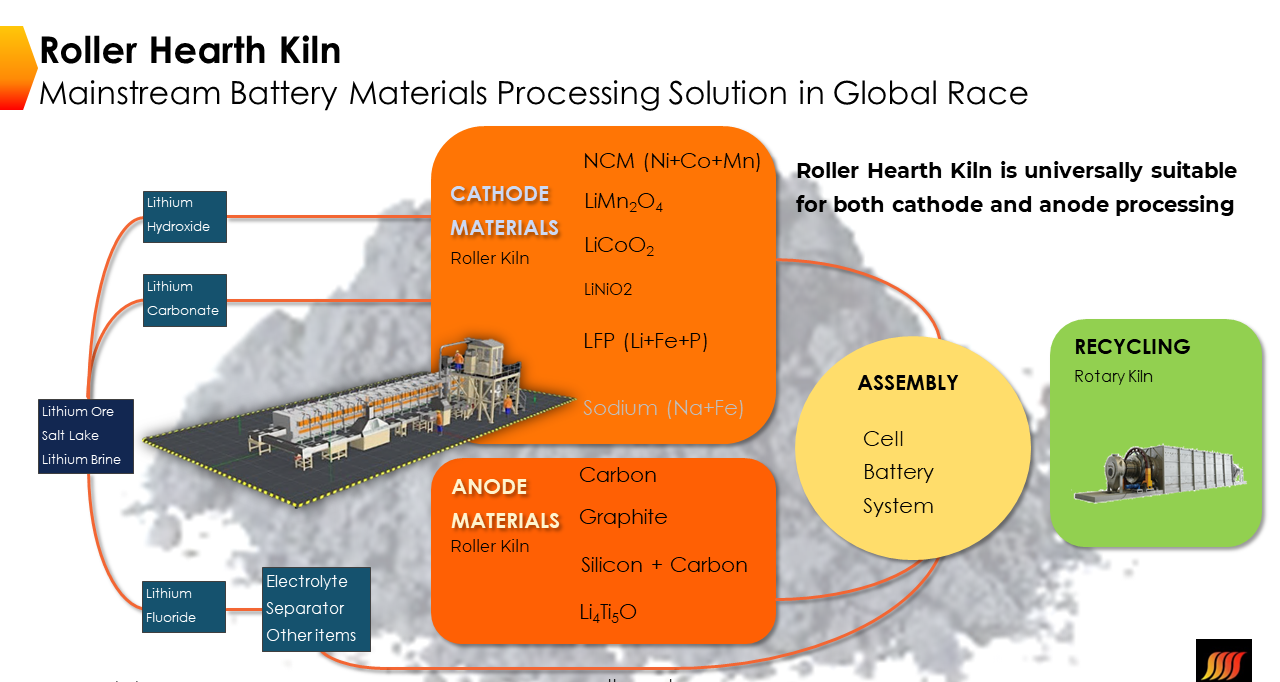
A Tri-Party signing of a Memorandum of Understanding (MOU) with Hengli and Honeystone and Therser UK that was executed at the recent LIBE 2023 conference in Budapest.
Hengli Eletek Co. Ltd was founded in 1992 with a dedicated focus on advancing pivotal equipment, such as electric heating, environmental protection, and plating systems. The company is steadfast in enhancing and broadening specialized equipment and system integration with process excellence at its core, aspiring to emerge as a leading force within the industry.
Therser (UK) Ltd was established in March 2009, marking the beginning of its journey. Rooted in history, with the acquisition of the Wellman Furnaces brand, our lineage extends back to 1904. This amalgamation incorporates extensive expertise and technology dedicated to the production of Kilns and Furnaces.
Honeystone has over 20 years of experience in capital equipment sales and services to clients in East and West Europe, South America and the US. Large installed base of hybrid and packaging equipment, especially in the area of MCM and power electronics, RF devices packaging, LTCC and thick film hybrids.
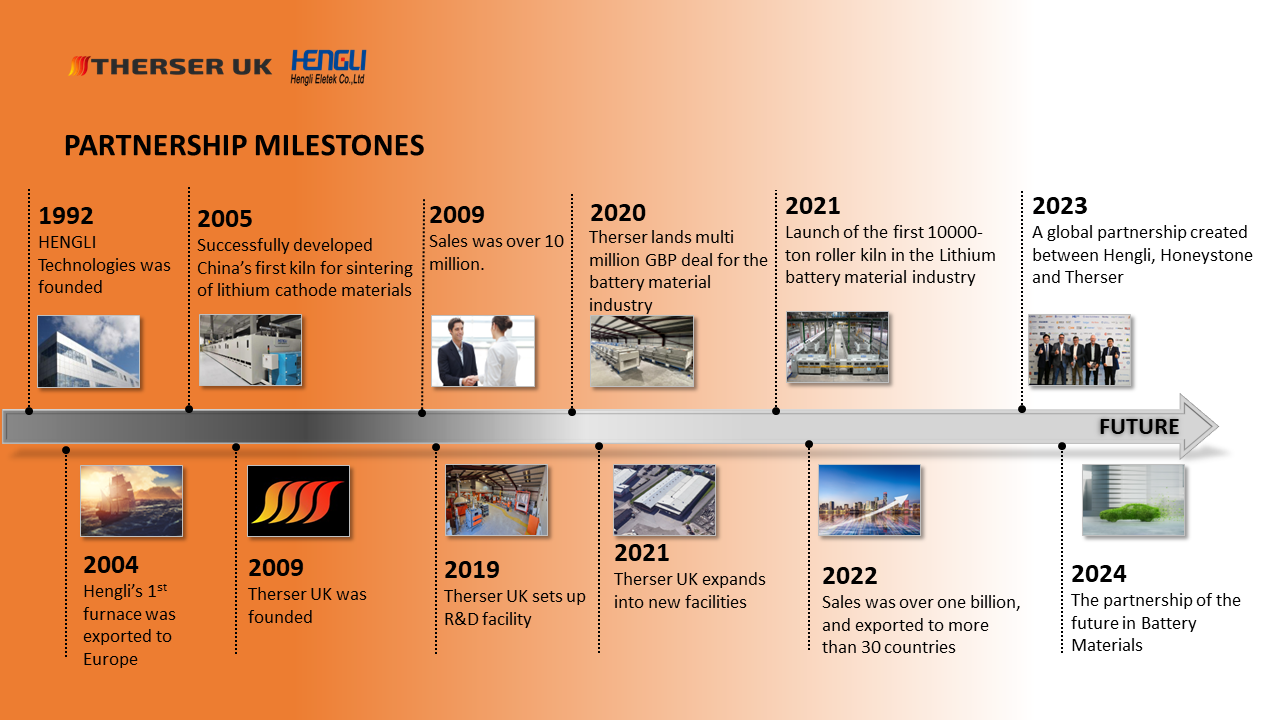
Our Turnkey Solution includes Engineering and System Design for integration of RHK into a complete production line.
- Slurry and Wet Milling
- Jet Milling
- Spray Drying
- Powder Handling
- Integration and fine tuning
- Air and water treatment
Collaboration between Therser and HengLi will set a unique precedent on the market by the benefits we offer to our customers
- Industry-approved, over 300 units in operation
- A synergy of design and control systems features
- Full compliance with local engineering codes, electrical and operators’ safety
- One stop shop turnkey supply
- Uniquely short lead-times
- Aggressive pricing
- Pilot size RHK installed in the USA by Therser supervision team
- Joint supply projects are being discussed in Europe, India, Australia, USA and North Africa
- Laboratory scale chamber ovens HXF and HXL series (for LFP and NMC chemistries) have been certified in CE and UK
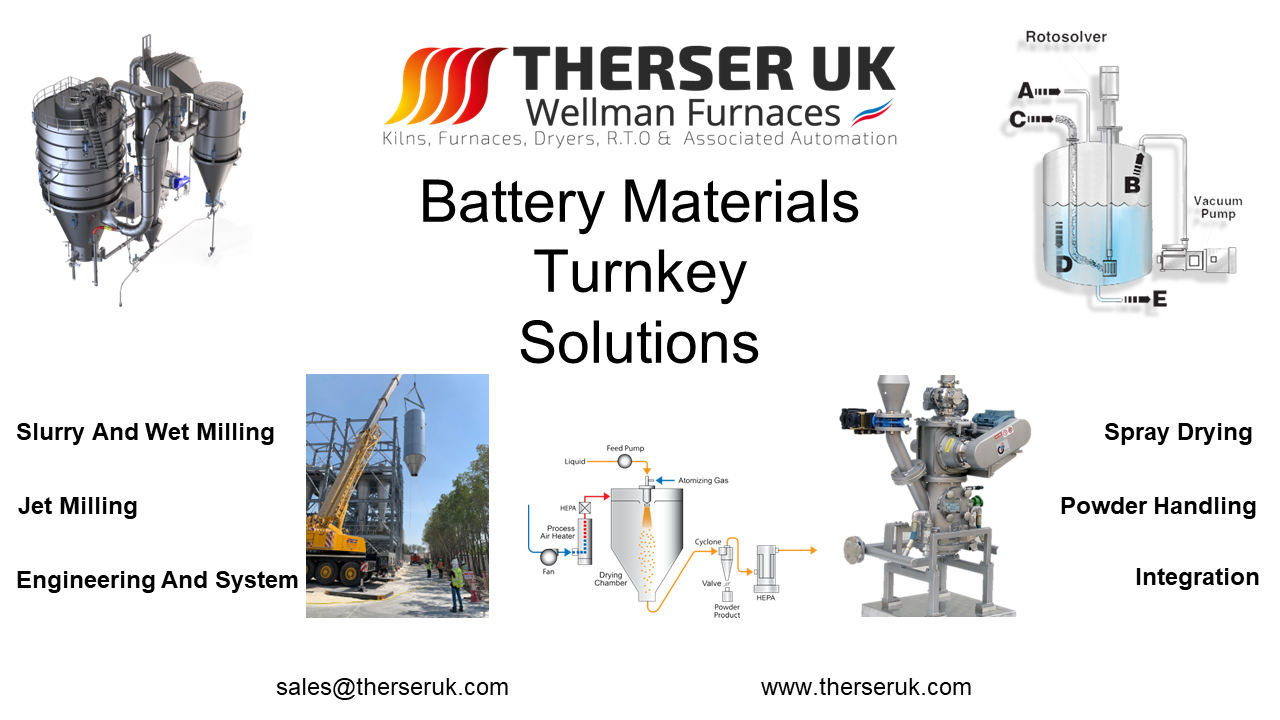
Kilns, Furnaces, and Process Equipment for Cathode Active Material Production
In the world of advanced battery technology, the production of cathode active materials (CAMs) plays a critical role in determining the performance, safety, and longevity of batteries. As the demand for electric vehicles (EVs), renewable energy storage, and portable electronics continues to surge, so does the need for high-quality cathode materials. Central to this production process are kilns, furnaces, and various process equipment, which are essential for achieving the desired chemical compositions, particle sizes, and morphologies.
Understanding Cathode Active Materials (CAMs)
Cathode active materials are the core components of a battery's cathode, where the electrochemical reactions occur during charging and discharging. The performance of a battery, including its energy density, cycle life, and thermal stability, is largely determined by the quality of these materials. Common CAMs include lithium cobalt oxide (LiCoO₂), lithium iron phosphate (LiFePO₄), and nickel manganese cobalt oxide (NMC), each with its unique properties suited for different applications.
The production of CAMs involves a series of complex chemical reactions and thermal treatments that must be carefully controlled to ensure the final product meets the required specifications. This is where kilns, furnaces, and specialized process equipment come into play.
The Role of Kilns in CAM Production
Kilns are essential for the calcination process, where precursor materials are heated to high temperatures in an oxygen-rich environment. This step is crucial for the formation of the final crystalline structure of the cathode material. The temperature, atmosphere, and duration of the calcination process must be precisely controlled to achieve the desired phase purity, particle size distribution, and chemical composition.
Rotary kilns, for example, are widely used in the production of CAMs due to their ability to provide uniform heat distribution and continuous processing. These kilns rotate slowly, ensuring that the material inside is evenly exposed to the high temperatures, leading to a consistent and high-quality product. Additionally, the ability to control the atmosphere within the kiln—whether it be oxidative, reductive, or inert—is vital for producing CAMs with the correct oxidation state and stoichiometry.
The Importance of Furnaces in Thermal Processing
Furnaces, like kilns, are used in the thermal processing of cathode materials, but they often operate at higher temperatures and are designed for specific processing needs. For instance, a sintering furnace is crucial for the densification of cathode powders, where particles are heated just below their melting point to promote bonding without losing their individual properties.
Controlled-atmosphere furnaces are particularly important in the production of CAMs that require specific gas environments to achieve the desired chemical composition. For example, some lithium-based cathode materials require a lithium-rich atmosphere to prevent lithium loss during the high-temperature processing steps. This precise control over the furnace environment ensures that the final cathode material possesses the correct stoichiometry and crystallinity, which are critical for battery performance.
Process Equipment: From Mixing to Milling
Beyond kilns and furnaces, other process equipment is equally vital in the production of CAMs. This includes mixers, mills, and dryers, each playing a crucial role in the preparation of the precursor materials before they enter the thermal processing stage.
Mixers are used to combine various raw materials, such as metal oxides and lithium compounds, to create a homogeneous mixture. This step is essential for ensuring that the final product has a uniform composition, which directly affects the battery's performance. High-shear mixers or planetary mixers are often employed to achieve this homogeneity, especially when dealing with materials that are difficult to mix.
Milling equipment, such as ball mills, is used to reduce the particle size of the mixed precursors. Fine particle sizes are critical for ensuring a high surface area, which improves the reaction kinetics during battery operation. The milling process must be carefully controlled to avoid introducing impurities or causing unwanted reactions.
Drying equipment, on the other hand, is used to remove any residual moisture from the precursors before they undergo thermal processing. Moisture can lead to unwanted reactions during calcination or sintering, affecting the purity and performance of the final CAM.
Innovations and Challenges in CAM Production
As the demand for better performing and more sustainable batteries grows, the production of CAMs is under constant innovation. Manufacturers are developing advanced kilns and furnaces with improved temperature control, energy efficiency, and atmosphere management capabilities. Additionally, new process equipment is being designed to handle the increasingly complex chemistries of next-generation cathode materials, such as solid-state batteries and high-nickel NMCs.
However, challenges remain. The production of CAMs is energy-intensive, and the push for greener manufacturing processes is driving the development of more energy-efficient kilns and furnaces. Moreover, as the industry moves towards recycling and reusing battery materials, process equipment must be adapted to handle recycled feedstocks, which often have different properties compared to virgin materials.
Kilns, furnaces, and process equipment are the unsung heroes in the production of cathode active materials, playing a critical role in the advancement of battery technology. As the world transitions to a more electrified future, the demand for high-performance batteries will continue to drive innovation in the production of CAMs. By understanding and optimizing the equipment and processes involved, manufacturers can produce better, safer, and more sustainable batteries, paving the way for the next generation of energy storage solutions.
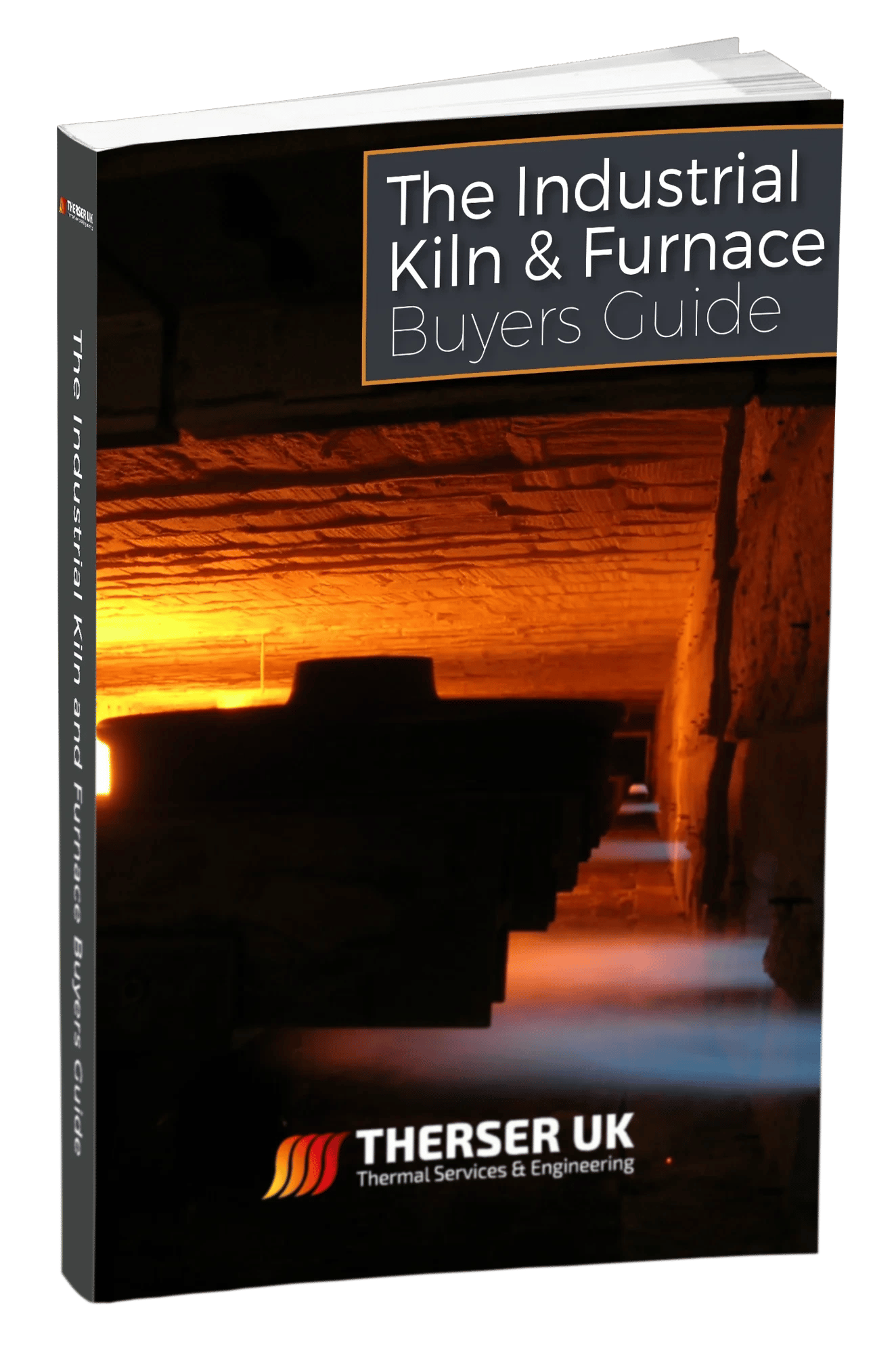
DOWNLOAD THE INDUSTRIAL KILN & FURNACE BUYERS GUIDE
If you need, or may need in the future, to invest in an industrial kiln, furnace or oven, then get a copy of this FREE guide today.
Discover:
- How to choose the right type of kiln or furnace
- How to avoid the most common mistakes with industrial kilns and furnaces
- How to ensure maximum fuel efficiency
So confirm your correct email address using the form provided and your copy will be in your inbox within seconds!
OUR CERTIFICATIONS
REVIEWS
TALK TO US TODAY
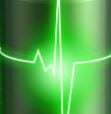
